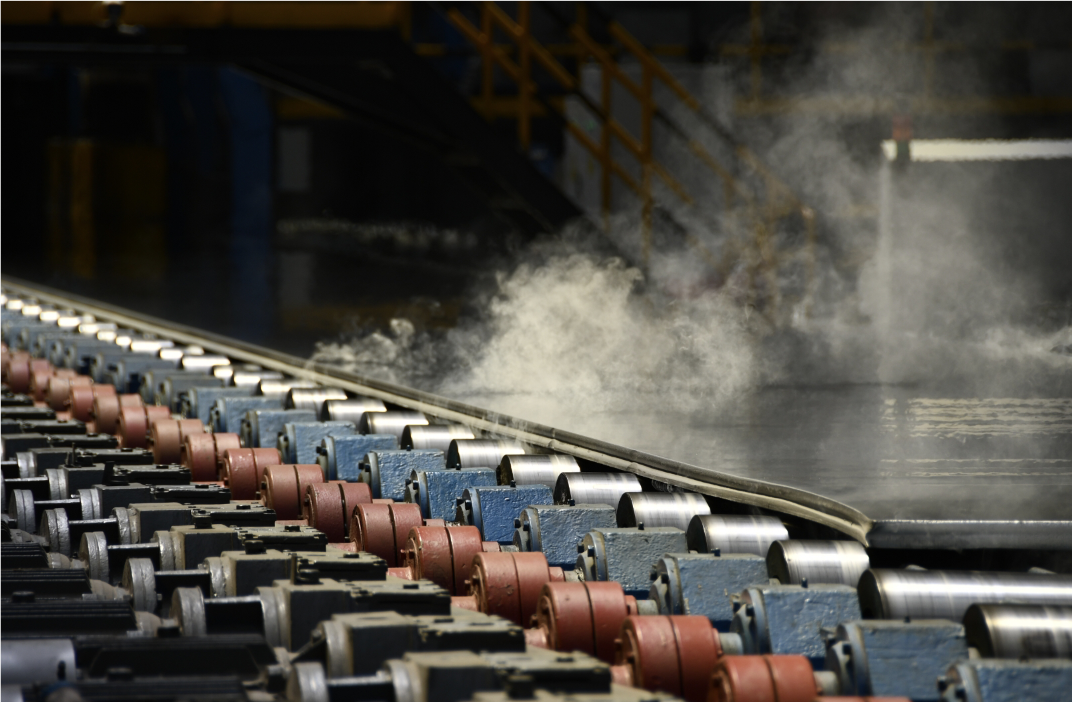
Marine Aluminium: 5052 vs 5083 Alloys Comparison
Sample: A4 Sized
Payment Terms: L/C,D/P,T/T
Delivery time: Within 15-30 Days
Email Us:sale06@mingtai-al.com
Marine Aluminium alloys are specialized materials designed to withstand harsh marine conditions. Due to their excellent resistance to seawater corrosion, high strength-to-weight ratio and ease of manufacturing, these alloys are often used in shipbuilding, offshore structures and marine equipment.
Marine aluminum usually belongs to the 5xxx series aluminum, with magnesium as the main component. The addition of magnesium not only improves strength, but also achieves long-term corrosion protection through a dense oxide layer. Compared with metals that are prone to rust, its lightweight properties can also reduce ship energy consumption, making it an ideal choice for modern shipbuilding and marine engineering.
Marine Aluminum: 5052 vs. 5083 – Which Alloy is Best for Your Project?
When selecting aluminum for marine applications, choosing the right alloy is critical for performance, durability, and cost-efficiency. Two of the most popular marine-grade aluminum alloys—5052 and 5083—offer excellent corrosion resistance, but they differ in strength, weldability, and ideal use cases.
5052 and 5083 Aluminum Alloys
Marine Grade aluminum 5052
Alloy Type: Al-Mg (Magnesium primary alloying element)
Strength: Moderate (good for lightweight structures)
Corrosion Resistance: Excellent, especially in saltwater
Weldability: Very good
Formability: Highly formable
Marine Grade aluminum 5083
Alloy Type: Al-Mg-Mn
Strength: Very high (superior for structural marine use)
Corrosion Resistance: Outstanding, even in harsh marine environments
Weldability: Good
Formability: Moderate (less flexible than 5052)
Key Differences: 5052 vs 5083 Aluminum
Property | 5052 Aluminum | 5083 Aluminum |
---|---|---|
Tensile Strength | 193–228 MPa (Moderate) | 270–310 MPa (Very High) |
Corrosion Resistance | Excellent | Exceptional (best for seawater) |
Weldability | Easy (ideal for fabrication) | Good (but needs proper technique) |
Formability | Excellent (easy to bend) | Moderate (less flexible) |
Cost | Lower | Higher (due to strength) |
Best Applications for Each Alloy
When to Use 5052 Aluminum:
Boat hulls & decks (where formability is key)
Marine fuel tanks & piping
Lightweight cabin structures
Sheet metal work & decorative marine trim
When to Use 5083 Aluminum:
Shipbuilding & offshore platforms (high-stress areas)
High-performance boat hulls (speedboats, military vessels)
Marine frames & structural supports
Subsea components (due to superior corrosion resistance)
Which Marine Aluminium Should You Choose?
Choose 5052 if: You need a cost-effective, easy-to-work alloy for lightweight marine structures.
Choose 5083 if: You require maximum strength and corrosion resistance for heavy-duty marine applications.
For most small boats and fabrication projects, 5052 is sufficient, while 5083 is preferred for commercial ships, naval vessels, and harsh environments.