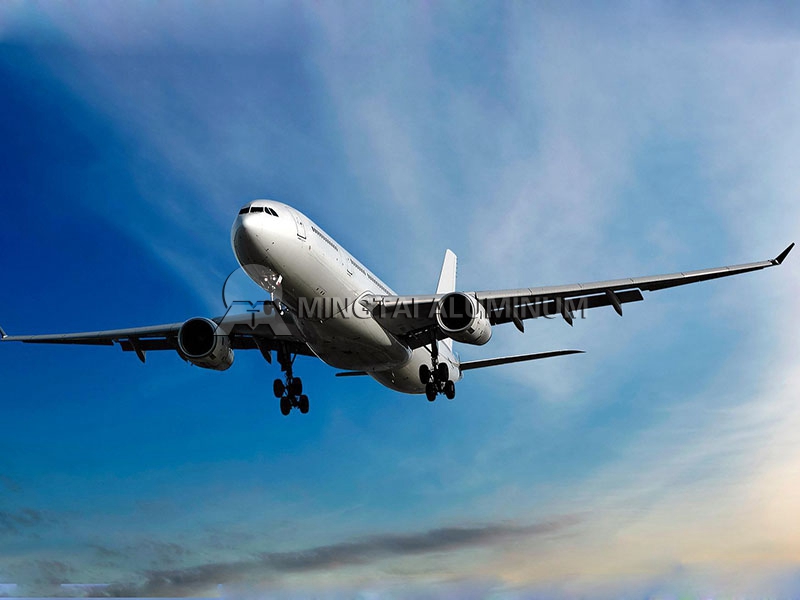
Aviation Aluminum
Sample: A4 Sized
Payment Terms: L/C,D/P,T/T
Delivery time: Within 15-30 Days
Email Us:sale06@mingtai-al.com
Introduction to Aviation Aluminum:
7000 series aluminum alloy, representing 7075 aluminum mainly contains zinc. Also belongs to the aviation series, is aluminum magnesium zinc copper alloy, is a heat treatable alloy, belongs to super hard aluminum alloy, has good wear resistance.
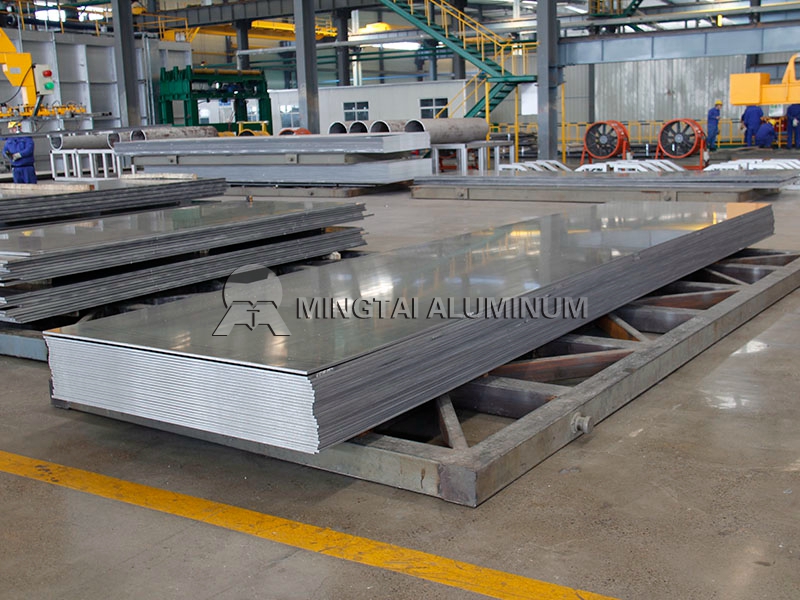
States of Aviation Aluminum:
The state of 7075 aluminum includes O state, a T6 state, a T651 state, a T6511 state, a T73 state, a T7351 state, a T7651 state, a T76511 state, and an H13 state.
Details of Aviation Aluminum:
7 series aluminum alloy is another commonly used alloy with a wide variety. It contains zinc and magnesium. The most common aluminum alloy is 7075 aluminum, but it can’t be welded, and its corrosion resistance is quite poor. Many CNC cutting parts use 7075 alloy. Zinc is the main alloying element in this series, and a small amount of magnesium alloy allows the material to be heat treated to very high strength properties. This series of materials are generally added with a small amount of copper, chromium and other alloys, of which the number 7075 aluminum alloy is especially top grade, the highest strength, suitable for aircraft frames and high-strength accessories.
The 7-series aluminum alloy is Al-Zn-Mg-Cu super-hard aluminum. This alloy was used in the aircraft manufacturing industry in the late 1940s. It belongs to Aviation aluminum and is still widely used in the aviation industry. Deformed aluminum alloy. It is characterized by good plasticity after solution treatment, particularly good heat treatment strengthening effect, high strength below 150 °C, and particularly good low temperature strength; poor weldability; stress corrosion cracking tendency; need to be coated with aluminum or other Protection processing is used. Two-stage aging improves the ability of the alloy to resist stress corrosion cracking. The plasticity in the annealed and quenched state is slightly lower than the same state of 2A12. Slightly better than 7A04, the static fatigue of the sheet. Notch sensitive, stress corrosion performance is better than 7A04. Density is 2.75.
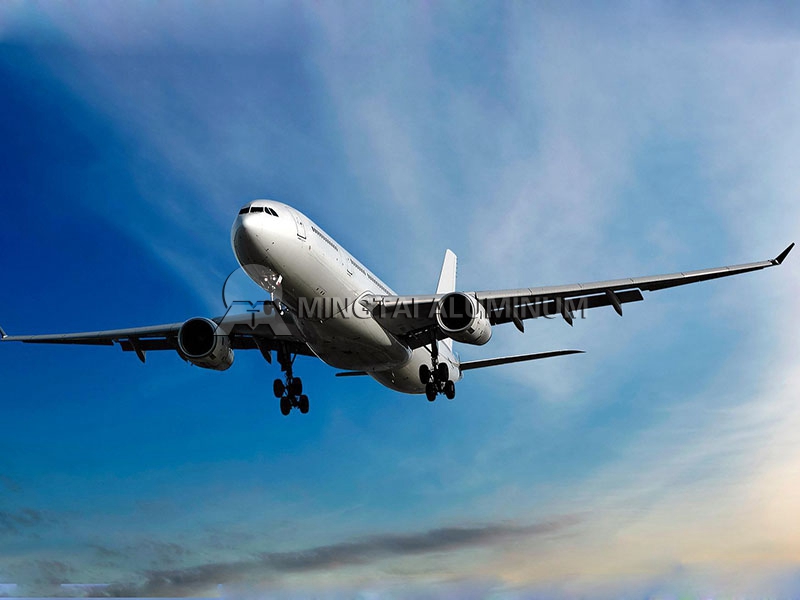
Features of Aviation Aluminum:
1. High strength and heat treatable alloy.
2. Good mechanical properties.
3. Good usability.
4. Easy to process and good wear resistance.
5. Good corrosion resistance and oxidation resistance.
6.T7351 state enhances corrosion crack resistance
7. High-strength materials for high-pressure structural parts.
7075 materials are generally added with a small amount of copper, chromium and other alloys. The A7075-aluminum alloy is especially top grade.
Known as the best product in aluminum alloy, it is high in strength and far superior to any mild steel. This alloy has good mechanical and anodic reaction.
Representative uses include aerospace, mold processing, mechanical equipment, fixtures,
It is especially used in the manufacture of aircraft structures and other high-stress structures that require high strength and corrosion resistance.
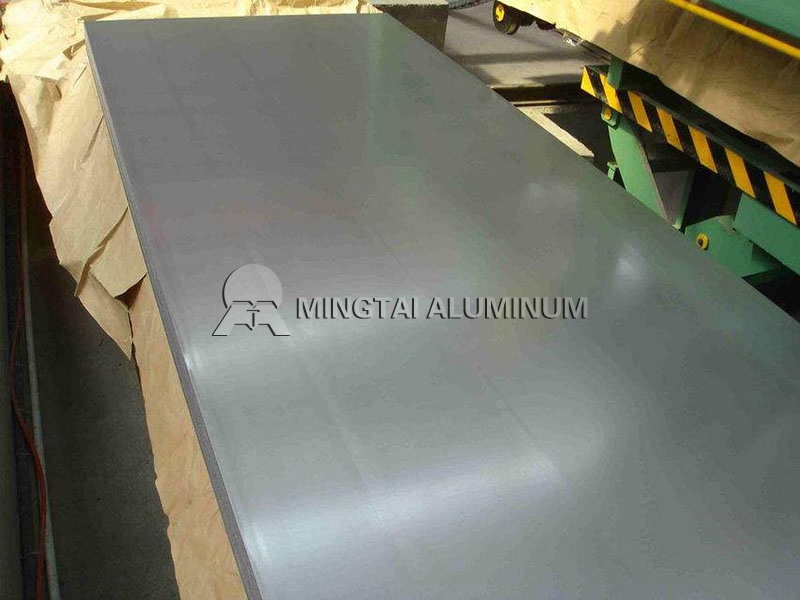
Main Use of Aviation Aluminum:
Aerospace fixtures, trucks, tower buildings, boats, pipelines and other areas of construction that require strength, weldability and corrosion resistance. Such as: aircraft parts, gears and shafts, fuse parts, instrument shafts and gears, missile parts jump valve parts, turbines, keys, aircraft, aerospace and defense applications.
Technical Parameters of Aviation Aluminum:
Typical alloy | 7075 aluminum plate |
Material status | F、O、T6、T651、T7451、H112, etc. |
Thickness (mm) | 1-500 |
Width (mm) | <2600 |
Length (mm) | <8000 |
Typical product | Aerospace industry, Golf ball head, Molds, Precision parts, etc. |